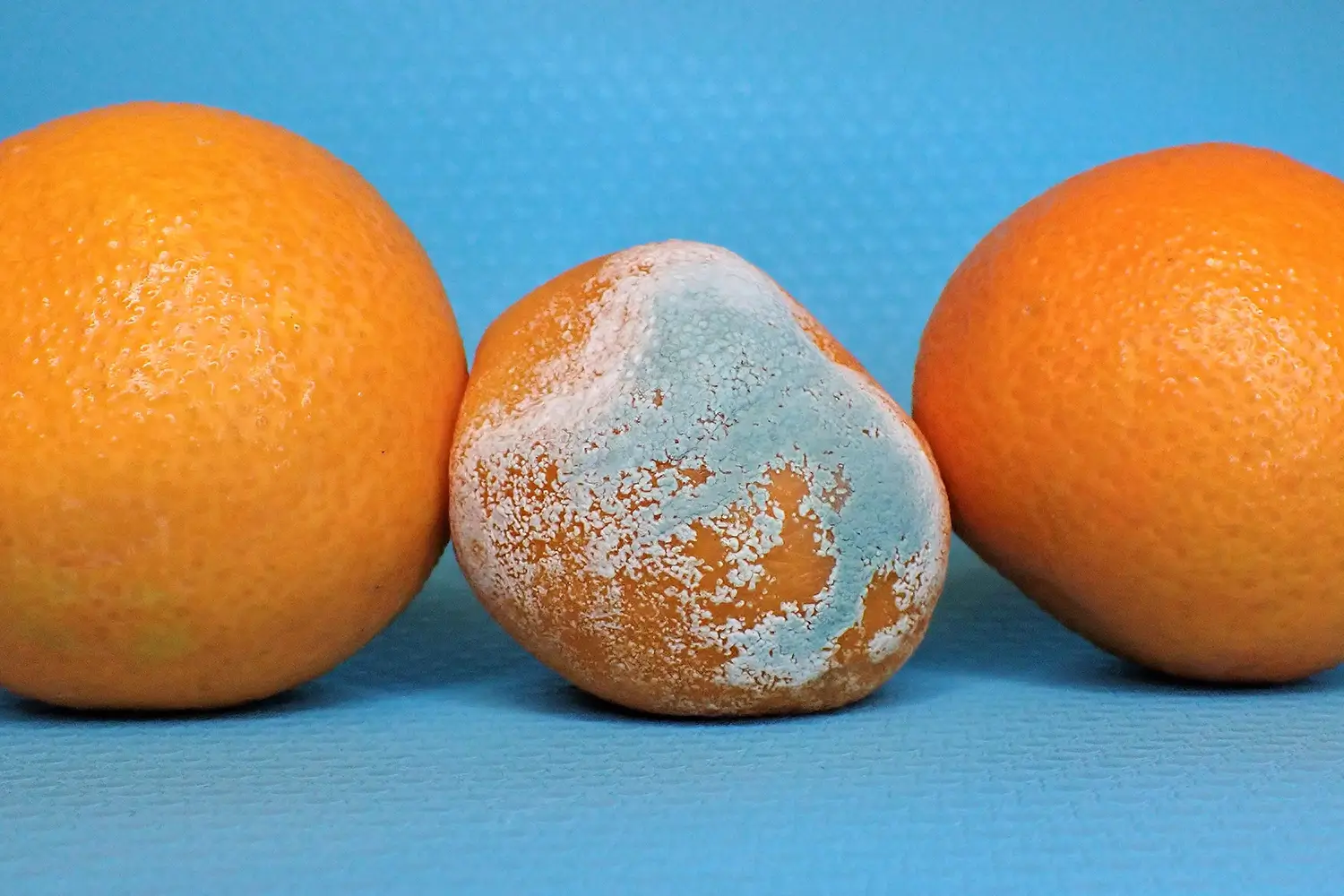
95 % Ausschuss-Reduktion und 500.000 € Einsparung? Steigerung der Produktqualität durch automatisierte Qualitätskontrolle
Es ist eigentlich eine ganz einfache Formel: Die schlechte Qualität eines Produkts führt zu einer nachhaltigen Schädigung der Beziehung zum Kunden oder zur Kundin. Ist die Qualität eines Produkts hoch, stellt sich meist eine nachhaltige Kundenbeziehung ein. Doch die Qualität eines Produkts dauerhaft erhöht zu halten, hängt von vielen Variablen ab. Idealerweise stützt sie sich auf eine automatisierte Qualitätskontrolle.
Produktqualität ist vor allem von einer ausgezeichneten Prozessqualität abhängig. Prozessqualität bedeutet, Ausschuss zu reduzieren. Predictive Quality, also die datengestützte Optimierung der Prozess- und Produktqualität, ist deshalb ein unverzichtbares Instrument zur Steigerung der Produktqualität. Das amerikanische Unternehmen Hill’s Pet Nutrition hat dies zum Beispiel längst erkannt.
KI-gestütztes Predictive Quality System am Beispiel Tiernahrungsprodukte
Hill's Pet Nutrition stellt Tiernahrungsprodukte her. Die Geschäftsstrategie schreibt häufige Neuanläufe und Produktumstellungen vor. Bei jeder Einführung und Umstellung steht das Produktentwicklungsteam vor der Herausforderung, das neue Produkt nach strengen Qualitätsstandards für Feuchtigkeit, Fett, Proteingehalt und Dichte zu produzieren. In der Vergangenheit waren bei jeder Umstellung manuelle Tests erforderlich, die jeweils 40 Minuten in Anspruch nahmen. Erst nach dieser Analyse konnten Anpassungen in den Einstellungen der Anlage vorgenommen werden.
Das KI-gestützte Predictive Quality System gibt eine Vorhersage für das Ergebnis des manuellen Tests aus. Darauf basierend werden dem Produktionsteam Vorschläge in Echtzeit geliefert, wie die Einstellungen der Anlage angepasst werden sollten, um die geforderte Produktqualität sicherzustellen, noch bevor finale Labordaten zur Verfügung stehen. Wenn die vorgeschlagenen Einstellungen vorgenommen wurden, sind lediglich abschließende und weniger zeitintensive Tests erforderlich. Der Einsatz von Predictive-Quality-Technologien und automatisierter Qualitätskontrolle führte zu einer deutlichen Reduktion des Ausschusses und steigerte den CpK-Wert (wichtigste Kenngröße für die Beschreibung der Fähigkeit von Prozessen) um die Hälfte. Das bedeutet, dass sich der Ausschuss um rund 95 % reduzierte.
Was ist Predictive Quality?
Predictive Quality, auch prädiktive Qualitätssicherung, kommt im Rahmen von Data Science und Predictive Analytics zum Einsatz. Ziel ist die kontinuierliche Prozessoptimierung auf Basis von automatisierten Vorhersagen. Für die Qualität eines Produkt werden diverse Parameter herangezogen. Von der spezifizierten Toleranzgrenze einer Einzelteilfertigung bis hin zu Umgebungsbedingungen wie der relativen Luftfeuchte können individuelle Parameter zu Problemen am Produkt führen.
Predicitive Quality ermöglicht die automatisierte Qualitätskontrolle und somit Überwachung sämtlicher Produktionsparameter. Eine Voraussage über etwaige Qualitätsmängel am Produkt wird auf Basis der Wechselwirkungen getroffen. Deshalb ist es möglich, noch vor der Fertigstellung eines Produkts Korrekturen vorzunehmen und Einstellungen zu verändern. Das führt zu massiven Zeit- und Kosteneinsparungen.
Maßgebliche Ziele von Predictive Quality
Das generelle Ziel von Predictive Quality, oder auch prädiktive Qualitätssicherung, ist stets die Optimierung der Qualität, indem Vorhersagen als Entscheidungsgrundlagen für weitere Maßnahmen herangezogen werden. Doch vor allem zwei Hauptziele lassen sich benennen: automatisierte Qualitätskontrolle und Prozessparameteroptimierung.
Die automatisierte Qualitätskontrolle ermöglicht eine Beurteilung in 50 bis 600 Millisekunden, abhängig von den jeweiligen Anforderungen, und sticht das menschliche Urteilsvermögen damit natürlich absolut aus. Sie ist auf Kosten und Nutzen optimiert, wobei das KI-Modell auch allgemeine Qualitätsanforderungen mit einbezieht.
In der Prozessparameteroptimierung lernt ein Modell die optimalen Modellparameter und wendet diese direkt an. Je nach Material oder Bauteil beispielsweise kommen individuell optimale Parameter zum Einsatz. Die Prozessparameteroptimierung ermöglicht eine automatische Parametereinstellung für minimierten Ausschuss.
Deep Learning KI-Modell am Beispiel von technischer Kunststofffolienproduktion
Am Unternehmen Toray Plastics lässt sich ein weiteres eindrückliches Beispiel für die Vorteile von Predictive Quality festmachen. Toray Plastics stellt eine Vielzahl von technischen Kunststofffolienprodukten für industrielle Anwendungen her. Jede Anwendung, jeder Kunde und jede Kundin hat eigene Spezifikationen und benötigt die entsprechenden idealen Betriebsbedingungen der Anlage. Jeder Folienbruch kostet Zehntausende von Dollar.
Mit einem IoT-Ansatz wurden in Echtzeit 400 Kennzahlen erfasst. Die relevanten Kennzahlen je Anlage konnten durch den Einsatz eines Deep Learning KI-Modells identifiziert und ausgewertet werden. Im Ergebnis erhalten die Produktionsteams kontinuierliche Statusberichte über mögliche Fehlerquellen und eine Risikoanalyse für Folienbrüche. Entsprechend schnell können Anpassungen vorgenommen werden. Die Anlageneffektivität wurde durch die automatisierte Qualitätskontrolle von rund 85 % auf über 90 % verbessert und jährlich werden über 500.000 Euro in Material- und Betriebskosten eingespart.
Standardisierter Ansatz für KI-gestützte Predictive-Quality-Lösungen
Produktionsleitende, Standortleitende und Predictive-Quality-Experts sind sich einig, dass als mittelfristiges Ziel eine bessere Produktqualität durch bessere Prozessqualität stehen muss. Jedes Unternehmen setzt zwar hochindividuelle Parameter für die Optimierung seiner Produkte. Doch eine Grundvoraussetzung für die Erhöhung der Produktqualität ist ein standardisierter Ansatz zur Erfassung und Weiterverarbeitung von Daten. Ein solcher Standard ermöglicht die schnelle und kostengünstige Umsetzung eines Proof of Concept, mit dem die Wirkung der geplanten Maßnahmen vorab überprüft werden kann.
Data Management jedoch gehört nicht originär zu den Aufgaben von Produktions- und Standortleitenden. Die Erfassung, Verarbeitung, Analyse und Verwendung von Daten ist ein eigenständiger Aufgabenbereich, der bei fehlenden internen Ressourcen auch gut von externen Spezialisten und Spezialistinnen übernommen werden kann. Ein ausgebildetes Data Team, bestehend aus Data Consultants und Data Engineers, erfasst Daten und testet KI-Lösungen m laufenden Betrieb und erzielt bereits während dieser Testphase schnelle und tiefgehende Ergebnisse.
Predictive-Quality-Prozesse benötigen cloudbasierte Hintergrundarchitektur
Ein weiterer wichtiger Baustein für die Etablierung von Predictive-Quality-Prozessen ist eine individualisierte Hintergrundarchitektur. Anlagen verändern sich permanent, indem zum Beispiel neue Maschinen hinzukommen, neue Produktionslinien eingeführt werden oder Zulieferer das Portfolio ergänzen. Bauen Unternehmen also nur für heute, sind sie morgen bereits abgehängt. Selbstlernende Systeme hingegen passen sich kontinuierlich an.
Die Hintergrundarchitektur sollte cloudbasiert sein. So ist sie flexibel zu organisieren und Kosten im Rahmen der Datenverarbeitung entstehen nur für wirklich notwendige Aktionen. Die Kosten für das gesamte System werden nach tatsächlicher Aufwendung einzelnen Produktionslinien zugeordnet und bleiben damit einsehbar. Maximale Transparenz ist somit sichergestellt.
Herausforderungen für erste Projekte mit Predictive Quality
Datenerfassung, Datenaufbereitung und Datenkombination sind grundsätzliche Themen, die im Vorfeld eines jeden Predictive-Quality-Projekts organisiert werden müssen. Denn Daten bilden die Grundlage für jeden lernenden Algorithmus. Wie die damit zusammenhängenden Herausforderungen gemeistert werden beschreibt der Artikel “Predictive Maintenance als Projekt” ausführlich.
Weitere Komponenten für erfolgreiche Predictive-Quality-Projekte
Predictive Quality basiert auf unternehmensspezifischen Anforderungen und erfordert somit einen detaillierten Blick für das Machbare und Sinnvolle. Die folgenden Komponenten eines entsprechenden Projekts hängen von zahlreichen Faktoren ab und sind immer wieder neu zu bewerten.
Automatisierte Qualitätskontrolle
Die automatisierte Qualitätskontrolle ist nicht immer relevant und anwendbar. Ihr Einsatz ist vor allem dann interessant, wenn die Qualitätskontrolle visuell stattfindet und noch nicht automatisiert ist.
Maschinelles Lernen
Das Maschinelle Lernen eignet sich, um den Zusammenhang von Maschinenparametern, Einstellungen und externen Parametern zu identifizieren. So lassen sich komplexe Muster entdecken. Durch eine Excel-Analyse beispielsweise lassen sich keine Gesetzmäßigkeiten entdecken. KI kann das sehr wohl. Dadurch entsteht eine Vorhersage der Produktqualität.
Umkehrung
Eine neue KI kann passende Einstellungen für industrielle Anlagen lernen, um geforderte Kennzahlen zu liefern. Sowohl Qualitätskennzahlen, als auch allgemeine Prozesskennzahlen können als Ziel gesetzt werden. Eine Anlage kann auf diese Weise nicht nur die geforderte Qualität liefern, sondern gleichzeitig den Wartungsaufwand gering halten.
Und nun? Proof of Concept als optimaler Projektstart
Ist die Entscheidung für Predictive Quality klar, obwohl noch Unsicherheit über die vorhandenen oder benötigten Rahmenbedingungen besteht, lohnt sich ein Testballon. Ein Proof of Concept ist wie bereits erwähnt relativ schnell vorbereitet und umgesetzt, integriert das Thema Datenorganisation und rollt es bei Bedarf neu auf, zeigt schnell erste Ergebnisse bereits innerhalb von im Durchschnitt vier Monaten und bewegt sich in einem kalkulierbaren Zeit- und Kostenrahmen.